Bitumen Emulsion
Bitumen emulsion is a liquefied type of bitumen with a low viscosity.
By dispersing bitumen in water and adding an emulsifier, ordinary bitumen turns into a low viscosity liquid that can easily be used in a variety of applications, including repairing and maintaining roads, waterproofing, spraying, etc.
Emulsions make it easy to handle, store, transport, and apply bitumen at a lower temperature.
Since this type of bitumen is liquid, there is no need to heat it before application.
Moreover, applying bitumen emulsions using cold techniques reduces energy consumption and makes road construction environmentally friendlier.
Are you interested in learning more about bitumen emulsion? Follow this article.
What is Bitumen Emulsion Composition?
Bitumen emulsion is a combination of water and bitumen.
As the mixture of water and oily products quickly separate, a third component, known as emulsifier, is normally added to the mixture in order to make it more stable.
Generally speaking, the amount of bitumen in the bitumen emulsion is 55 to 65%, the amount of water 35 to 45 %, and the amount of emulsifiers should be a maximum 0.5% of bitumen emulsion’s weight.
Emulsifiers are used for making a mixture of water and oil dispersed in each other.
In addition to their ability to reduce the tension between oil and water molecules, emulsifiers have an electronic charge that affects the molecules of bitumen emulsion and leads to categorizing it into Cationic and Anionic.
Cationic emulsifiers, for example, form a layer of positive charge around the bitumen droplets that prevent them from joining each other.
This makes bitumen dispersion in water more durable.
The electronic charge of bitumen emulsion decides on what kind of surface it should be used.
Some aggregates (such as marble aggregates) mix well with anionic bitumen emulsion and some others are a better solution to cationic bitumen emulsion (such as granite aggregates).
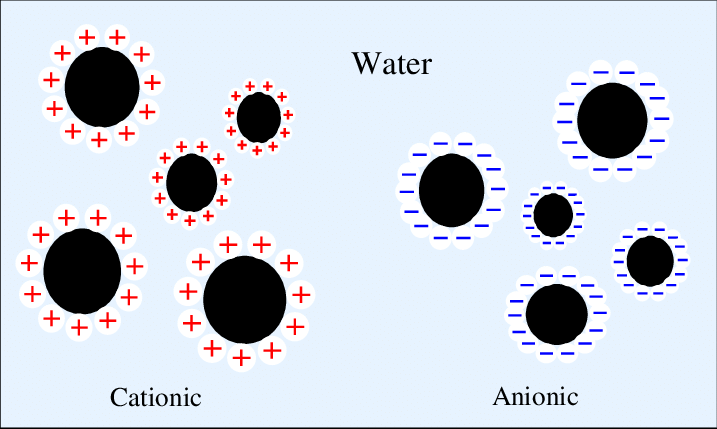
You might be wondering :
How is Bitumen Emulsion Manufactured?
Bitumen emulsion is usually made using a colloid mill, which mixes bitumen with water and emulsifier. In this process, bitumen is milled into very small droplets that can easily suspend in the water.
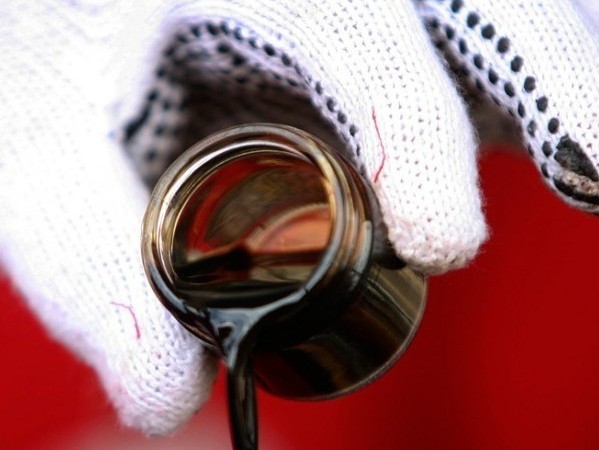
With the addition of emulsifiers, bitumen droplets become more water friendly. Water droplets also move closer to the tiny bitumen droplets, ensuring that the final bituminous product is stable enough.
In the manufacturing process, many factors such as droplets’ size, chemical addition, and the temperature of various components are accurately controlled.
The resulting bitumen has a consistent structure that makes it unique for various applications.
Check out Our Article about Bitumen Production Process
Different Types of Bitumen Emulsion
Various emulsions are classified based on two main factors:
- particles’ electrostatic charge
- breaking or setting time
In an emulsion, if the particles’ charge is negative, the bitumen emulsion is called Anionic and introduces itself with the letter “A”. Otherwise, the bitumen is known as cationic and has the “C” letter.
The second grading system of bitumen emulsion is closely related to the application. When applied to a surface, bitumen emulsion must break and set.
Technically, breaking means the evaporation of water, which makes bitumen strong enough for sticking to aggregates and setting on the place of application.
The time that is needed for bitumen emulsion to lose water and behave like an ordinary bitumen, is called the reactivity rate.
This parameter determines whether the bitumen is rapid setting emulsion, medium setting emulsion, and slow setting emulsion.
When bitumen emulsion is applied to a surface, choosing the right setting type is crucial. As previously said, there exist three types of the bitumen based on the setting time.
The first one is rapid setting emulsion which sets quickly in contact with aggregates; therefore, it is highly used in low surface of roads, particularly chip seals and surface dressing.
The second type is medium setting emulsion which is used in premixing of bitumen emulsion and coarse aggregate, particularly open graded mixes.
The last one is slow setting emulsion which sets very slowly. That’s why it is suitable for being mixed with aggregates of high surface area.
Slow setting emulsion is the most stable type of emulsion and can be used in dense graded aggregate bases, slurry seals, and recycling asphalt.
Another factor that can affect the reactivity of bitumen emulsion is the temperature of the surface onto which it is applied.
In hot weather, evaporation of water can accelerate.
Both cationic and anionic bitumen emulsions are categorized according to the setting time.
Look at the table below to find the various categories of bitumen emulsion and their globally standard names.
Bitumen Emulsion Types | ||
---|---|---|
Cationic Emulsion | Anionic Emulsion | |
Rapid setting type (RS) | CRS-1 CRS-2 CRS-1h K1-60 K1-40 K1-70 | RS-1 RS-2 |
Medium setting type (MS) | CMS-1 CMS-2 CMS-2h K2 K3 | MS-1 MS-2 MS-2h HFMS-1 HFMS-2 HFMS-2h HFMS-2S |
Slow setting type (SS) | CSS-1 CSS-1h Modified CSS-1h | SS-1 SS-1h Modified SS-1h |
An Explanation of Bitumen Emulsion Prefixes and Suffixes
Several numbers and letters are used to describe the characteristics of the emulsions.
The number 1 or 2 indicates the viscosity of the emulsion, with the number 1 meaning lower viscosity and number 2 meaning higher viscosity.
The “h” indicates a harder base bitumen (lower penetration grade) like penetration grade 30/40. In contrast, the “s” indicates a softer base bitumen like penetration grade 80/100 that is suitable for mixing with sand aggregates.
The HF prefix shows that the bitumen emulsion polymer emulsifying agent creates a gel structure in the bitumen residue.
The gel structure allows a thicker bitumen coating on the aggregate particles. This thicker film makes the surface more resistant to oxidation from exposure to the atmosphere.
Bitumen Emulsion Grades and Specifications
Bitumen emulsion is classified according to international standards, and their specifications through the bitumen standard tests are as follows:
Bitumen Emulsion CSS-1h Specifications | |||
---|---|---|---|
Specification | Test Method | Min. | Max. |
Cement Mixing % | ASTM D6935 | – | 2.0 |
Storage Stability in 24-H (%) | ASTM D6930 | – | 1 |
Sieve Test (%) | ASTM D6933 | – | 0.1 |
Viscosity Saybolt Furel At 50 °C | ASTM D7496 | 20 | 100 |
Particle Charge (None) | ASTM D7402 | Positive | |
Distillation | |||
Residue % | ASTM D6997 | 57 | – |
Test On Residue From Distillation Test | |||
Penetration, At 25 °C, 100 gr on 5 sec, (0.1 mm) | ASTM D5 | 40 | 90 |
Ductility, At 25 °C, 5 cm/min, (cm) | ASTM D113 | 40 | – |
Solubility in TCE, WT% | ASTM D2042 | 97.5 | – |
Bitumen Emulsion CMS-2 Specification | |||
---|---|---|---|
Property | Min | Max | Test Method |
Viscosity, Saybolt Furol at 50 °C, SFS | 50 | 450 | ASTM D244 |
Storage stability test, 24-h, % | – | 1 | ASTM D6930 |
Particle charge test | Positive | ASTM D244 | |
Sieve test, % | – | 0.1 | ASTM D6933 |
Coating ability and water resistance: | |||
Coating, dry aggregate | Good | – | ASTM D244 |
Coating, after spraying | Fair | – | ASTM D244 |
Coating, wet aggregate | Fair | – | ASTM D244 |
Coating, after spraying | Fair | – | ASTM D244 |
Distillation: | |||
Oil distillate, by volume of emulsion, % | – | 12 | ASTM D6997 |
Residue, % | 65 | – | ASTM D244 |
test on residue from distillation | |||
Penetration, 25°C (77°F), 100 g, 5 s | 100 | 250 | ASTM D5 |
Ductility, 25°C (77°F), 5 cm/min, cm | 40 | – | ASTM D113 |
Solubility in trichloroethylene, % | 97.5 | – | ASTM D2042 |
Bitumen Emulsion CMS-2h Specification | |||
---|---|---|---|
Property | Min | Max | Test Method |
Viscosity, Saybolt Furol at 50 °C, SFS | 40 | 450 | ASTM D244 |
Storage stability test, 24-h, % | – | 1 | ASTM D6930 |
Particle charge test | Positive | ASTM D244 | |
Sieve test, % | – | 0.1 | ASTM D6933 |
Coating ability and water resistance: | |||
Coating, dry aggregate | Good | – | ASTM D244 |
Coating, after spraying | Fair | – | ASTM D244 |
Coating, wet aggregate | Fair | – | ASTM D244 |
Coating, after spraying | Fair | – | ASTM D244 |
Distillation: | |||
Oil distillate, by volume of emulsion, % | – | 12 | ASTM D6997 |
Residue, % | 65 | – | ASTM D244 |
test on residue from distillation | |||
Penetration, 25°C (77°F), 100 g, 5 s | 40 | 90 | ASTM D5 |
Ductility, 25°C (77°F), 5 cm/min, cm | 40 | – | ASTM D113 |
Solubility in trichloroethylene, % | 97.5 | – | ASTM D2042 |
Bitumen Emulsion CRS-2 Specification | |||
---|---|---|---|
Property | Min | Max | Test Method |
Viscosity, Saybolt Furol at 50 °C, SFS | 100 | 400 | ASTM D244 |
Storage stability test, 24-h, % | – | 1 | ASTM D6930 |
Demulsibility, 35 mL, 0.8 % dioctyl sodium sulfosuccinate, % | 40 | – | ASTM D244 |
Coating ability and water resistance: | |||
Particle charge test | Positive | ASTM D244 | |
Sieve test, % | – | 0.1 | ASTM D6933 |
Distillation: | |||
Oil distillate, by volume of emulsion, % | – | 3 | ASTM D6997 |
Residue, % | 65 | – | ASTM D244 |
test on residue from distillation | |||
Penetration, 25°C (77°F), 100 g, 5 s | 100 | 250 | ASTM D5 |
Ductility, 25°C (77°F), 5 cm/min, cm | 40 | – | ASTM D113 |
Solubility in trichloroethylene, % | 97.5 | – | ASTM D2042 |
Bitumen Emulsion SS-1 Specification | |||
---|---|---|---|
Property | Min | Max | Test Method |
Viscosity SSF, 25 °C (s) | 20 | 100 | ASTM D244 |
Viscosity SSF, 50 °C (s) | – | – | ASTM D244 |
Storage stability, 24 h (%) | – | 1 | ASTM D6930 |
Demulcibility , 0.02 N CaCl2 (%) | – | – | |
Cement mixing (%) | – | 2 | |
Sieve (%) | – | 0.1 | ASTM D6933 |
Residue (%) | 57 | – | ASTM-D244 |
Solubility in trichloroethylene % | 97.5 | – | ASTM D2042 |
Penetration 77°F (25°C) 100g,5s mm | 100 | 200 | ASTM D5 |
ductility, 77°F (25 °C), 5cm/min (cm) | 40 | ASTM D113 |
Bitumen Emulsion SS-1h Specification | |||
---|---|---|---|
Property | Min | Max | Test Method |
Viscosity SSF, 25 °C (s) | 20 | 100 | ASTM D244 |
Viscosity SSF, 50 °C (s) | – | – | ASTM D244 |
Storage stability, 24 h (%) | – | 1 | ASTM D6930 |
Cement mixing (%) | – | 2 | |
Sieve (%) | – | 0.1 | ASTM D6933 |
Residue (%) | 57 | – | ASTM-D244 |
Solubility in trichloroethylene % | 97.5 | – | ASTM D2042 |
Penetration 77°F (25°C) 100g,5s mm | 40 | 90 | ASTM D5 |
Storage stability, 24 h (%) | 40 | ASTM D113 |
Bitumen Emulsion RS-1 Specification | |||
---|---|---|---|
Property | Min | Max | Test Method |
Viscosity SSF, 25 °C (s) | 20 | 100 | ASTM D244 |
Storage stability, 24 h (%) | – | 1 | ASTM D6930 |
Demulcibility , 35ml, 8% dioctyl sodium sulfosuccinate, % | 60 | – | |
Particle charge test | Minus | – | ASTM D244 |
Sieve (%) | – | 0.1 | ASTM D6933 |
Residue by distillation (%) | 55 | – | ASTM-D244 |
Residue penetration, 25 °C | 100 | 200 | ASTM D5 |
Solubility in trichloroethylene % | 97.5 | – | ASTM D2042 |
Residue ductility, 25 °C, 5cm/min (cm) | 40 | ASTM D113 |
Bitumen Emulsion RS-2 Specification | |||
---|---|---|---|
Property | Min | Max | Test Method |
Viscosity SSF, 25 °C (s) | 20 | 100 | ASTM D244 |
Storage stability, 24 h (%) | – | 1 | ASTM D6930 |
Demulcibility , 35ml, 8% dioctyl sodium sulfosuccinate, % | 60 | – | |
Particle charge test | Minus | – | ASTM D244 |
Sieve (%) | – | 0.1 | ASTM D6933 |
Residue by distillation (%) | 63 | – | ASTM-D244 |
Residue penetration, 25 °C | 100 | 200 | ASTM D5 |
Solubility in trichloroethylene % | 97.5 | – | ASTM D2042 |
Residue ductility, 25 °C, 5cm/min (cm) | 40 | ASTM D113 |
Bitumen Emulsion MS-2 Specification | |||
---|---|---|---|
Property | Min | Max | Test Method |
Viscosity SSF, 25 °C (s) | 20 | 100 | ASTM D244 |
Storage stability, 24 h (%) | – | 1 | ASTM D6930 |
Particle charge test | Minus | – | ASTM D244 |
Sieve (%) | – | 0.1 | ASTM D6933 |
Residue by distillation (%) | 65 | – | ASTM-D244 |
Residue penetration, 25 °C | 100 | 200 | ASTM D5 |
Solubility in trichloroethylene % | 97.5 | – | ASTM D2042 |
Residue ductility, 25 °C, 5cm/min (cm) | 40 | ASTM D113 |
Bitumen Emulsion MS-2h Specification | |||
---|---|---|---|
Property | Min | Max | Test Method |
Viscosity SSF, 25 °C (s) | 20 | 100 | ASTM D244 |
Storage stability, 24 h (%) | – | 1 | ASTM D6930 |
Particle charge test | Minus | – | ASTM D244 |
Sieve (%) | – | 0.1 | ASTM D6933 |
Residue by distillation (%) | 65 | – | ASTM-D244 |
Residue penetration, 25 °C | 40 | 90 | ASTM D5 |
Solubility in trichloroethylene % | 97.5 | – | ASTM D2042 |
Residue ductility, 25 °C, 5cm/min (cm) | 40 | ASTM D113 |
Bitumen Emulsion HFMS-1 Specification | |||
---|---|---|---|
Property | Min | Max | Test Method |
Viscosity, Saybolt Furol at 25 °C, SFS | 20 | 100 | ASTM D244 |
Storage stability, 24 h (%) | – | 1 | ASTM D6930 |
Particle charge test | Minus | – | ASTM D6936 |
Sieve (%) | – | 0.1 | ASTM D6933 |
Residue by distillation (%) | 55 | – | ASTM-D244 |
Residue penetration, 25 °C | 100 | 200 | ASTM D5 |
Residue ductility, 25 °C, 5cm/min (cm) | 40 | – | ASTM D113 |
Solubility in trichloroethylene % | 97.5 | – | ASTM D2042 |
Float of residue. 60 °C (s) | 1200 | ASTM D139 |
Bitumen Emulsion HFMS-2 Specification | |||
---|---|---|---|
Property | Min | Max | Test Method |
Viscosity, Saybolt Furol at 25 °C, SFS | 100 | – | ASTM D244 |
Storage stability, 24 h (%) | – | 1 | ASTM D6930 |
Particle charge test | Minus | – | ASTM D6936 |
Sieve (%) | – | 0.1 | ASTM D6933 |
Residue by distillation (%) | 65 | – | ASTM-D244 |
Residue penetration, 25 °C | 100 | 200 | ASTM D5 |
Residue ductility, 25 °C, 5cm/min (cm) | 40 | – | ASTM D113 |
Solubility in trichloroethylene % | 97.5 | – | ASTM D2042 |
Float of residue. 60 °C (s) | 1200 | ASTM D139 |
Bitumen Emulsion HFMS-2s Specification | |||
---|---|---|---|
Property | Min | Max | Test Method |
Viscosity, Saybolt Furol at 25 °C, SFS | 50 | – | ASTM D244 |
Storage stability, 24 h (%) | – | 1 | ASTM D6930 |
Particle charge test | Minus | – | ASTM D6936 |
Sieve (%) | – | 0.1 | ASTM D6933 |
Residue by distillation (%) | 65 | – | ASTM-D244 |
Solvents, by volume of emulsion | 1 | 7 | ASTM D6997 |
Residue penetration, 25 °C | 200 | – | ASTM D5 |
Residue ductility, 25 °C, 5cm/min (cm) | 40 | – | ASTM D113 |
Solubility in trichloroethylene % | 97.5 | – | ASTM D2042 |
Float of residue. 60 °C (s) | 1200 | ASTM D139 |
Bitumen Emulsion HFMS-2h Specification | |||
---|---|---|---|
Property | Min | Max | Test Method |
Viscosity, Saybolt Furol at 25 °C, SFS | 100 | – | ASTM D244 |
Storage stability, 24 h (%) | – | 1 | ASTM D6930 |
Particle charge test | Minus | – | ASTM D6936 |
Sieve (%) | – | 0.1 | ASTM D6933 |
Residue by distillation (%) | 65 | – | ASTM-D244 |
Residue penetration, 25 °C | 40 | 90 | ASTM D5 |
Residue ductility, 25 °C, 5cm/min (cm) | 40 | – | ASTM D113 |
Solubility in trichloroethylene % | 97.5 | – | ASTM D2042 |
Float of residue. 60 °C (s) | 1200 | ASTM D139 |
Bitumen Emulsion HFRS-2 Specification | |||
---|---|---|---|
Property | Min | Max | Test Method |
Viscosity, Saybolt Furol at 25 °C, SFS | 20 | 100 | ASTM D244 |
Storage stability, 24 h (%) | – | 1 | ASTM D6930 |
Particle charge test | Minus | – | ASTM D6936 |
Sieve (%) | – | 0.1 | ASTM D6933 |
Demulcibility , 35ml, 8% dioctyl sodium sulfosuccinate, % | 60 | – | ASTM D6933 |
Residue by distillation (%) | 63 | – | ASTM-D244 |
Residue penetration, 25 °C | 100 | 200 | ASTM D5 |
Residue ductility, 25 °C, 5cm/min (cm) | 40 | – | ASTM D113 |
Float of residue. 60 °C (s) | 1200 | ASTM D139 |
Bitumen Emulsion K1-70 Specifications | |||
---|---|---|---|
Specification | Test Method | Min. | Max. |
Storage Stability in 24-H (%) | ASTM D6930 | – | 1 |
Sieve Test (%) | ASTM D6933 | – | 0.1 |
Viscosity Saybolt Furel At 50 °C | ASTM D7496 | 20 | – |
Particle Charge (None) | ASTM D244-ASTM D7402 | Positive | |
Distillation | |||
Oil Distillate, by Volume of Emulsion, % | ASTM D6997 | – | 4 |
Residue, % | ASTM D6997 | 67 | – |
Test On Residue From Distillation Test | |||
Penetration, At 25 °C, 100 gr, 5 sec (0.1 mm) | ASTM D5 | 60 | 250 |
Ductility, At 25 °C, 5 CM/Min | ASTM D113 | 20 | – |
Solubility in TCE, WT% | ASTM D2042 | 97.5 | – |
Bitumen Emulsion CSS1 Specifications | ||
---|---|---|
Specification | Test Method | Value |
Binder Content or Bitumen Residue (%) | ASTM D6997 | ≥60 |
Cement Mixing Test (%) | ASTM D6935 | ≥2 |
Storage Stability in 24-H (%) | ASTM D6930 | 1≥ |
Sieve Test (%) | ASTM D6933 | 0.1≥ |
Viscosity Saybolt Furel At 50 °C | ASTM D7496 | ≥20 |
Demulsibility, 35 ml. 0.8% Dioctyl Sodium Sulfosuccinate (%) | ASTM D6936 | ≥40 |
Oil Distillate Content (%) | ASTM D6997 | 8≥ |
Tests On Residue From Distillation Test | ||
Penetration, At 25 °C, 100 gr on 5 sec (0.1 mm) | ASTM D5 | ≥50 |
Ductility, At 25 °C, 5 CM/Min | ASTM D113 | ≥40 |
Solubility in TCE, WT% | ASTM D2042 | ≥97.5 |
Bitumen Emulsion CRS-1 Specifications | |||
---|---|---|---|
Specification | Test Method | Min. | Max. |
Binder Content or Bitumen Residue (%) | ASTM D6997 | 63 | – |
Storage Stability in 24-H (%) | ASTM D6930 | – | 1 |
Sieve Test (%) | ASTM D6933 | – | 0.1 |
Viscosity Saybolt Furel At 50 °C | ASTM D7496 | 20 | – |
Particle Charge (None) | ASTM D244-ASTM D7402 | Positive | |
Test On Residue From Distillation Test | |||
Penetration, At 25 °C, 100 gr on 5 sec (0.1 mm) | ASTM D5 | 50 | – |
Ductility, At 25 °C, 5 CM/Min | ASTM D113 | 40 | – |
Solubility in TCE, WT% | ASTM D2042 | 97.5 | – |
Bitumen Emulsion K1-60 Specifications | |||
---|---|---|---|
Specification | Test Method | Min. | Max. |
Binder Content or Bitumen Residue (%) | ASTM D6997 | 63 | – |
Storage Stability in 24-H (%) | ASTM D6930 | – | 1 |
Sieve Test (%) | ASTM D6933 | – | 0.1 |
Viscosity Saybolt Furel At 50 °C | ASTM D7496 | 20 | – |
Particle Charge (None) | ASTM D244-ASTM D7402 | Positive | |
Test On Residue From Distillation Test | |||
Penetration, At 25 °C, 100 gr on 5 sec (0.1 mm) | ASTM D5 | 50 | – |
Ductility, At 25 °C, 5 CM/Min | ASTM D113 | 40 | – |
Solubility in TCE, WT% | ASTM D2042 | 97.5 | – |
Bitumen Emulsion K1-40 Specifications | |||
---|---|---|---|
Specification | Test Method | Min. | Max. |
Storage Stability in 24-H (%) | ASTM D6930 | – | 1 |
Sieve Test (%) | ASTM D6933 | – | 0.1 |
Viscosity Saybolt Furel At 25 °C | ASTM D7496 | – | 25 |
Particle Charge (None) | ASTM 244 | Positive | |
Distillation | |||
Residue % | ASTM D6997 | 37 | – |
Test On Residue From Distillation Test | |||
Penetration, At 25 °C, 100 gr on 5 sec (0.1 mm) | ASTM D5 | 60 | 200 |
Solubility in TCE, WT% | ASTM D2042 | 97.5 | – |
What Factors are Important in Grading Bitumen Emulsion?
1- Viscosity
The first vital factor for grading bitumen emulsion is the viscosity value. It is obtained by performing a viscosity test.
The viscosity of bitumen emulsion is determined by its bitumen content.
For dense graded aggregates, a lower viscosity of bitumen emulsion is needed; however, for open graded aggregates, a higher viscosity of bitumen emulsion should be used.
An emulsion with small droplet size and a narrow distribution will give a higher viscosity.
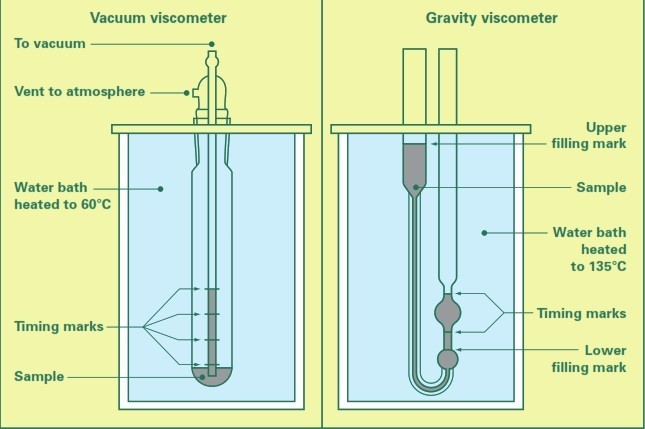
2- Ductility
To indicate the bitumen resistance to breaking, a ductility test is done.
This testing system measures the extent to which a sample of bitumen can stretch before breaking.
A bitumen emulsion that has a ductility of more than 40 cm makes the surface of a road safe and strong to heavy traffic and do not break easily. In cold weather bitumen with low ductility value may get cracked.
You can read more about different types of standard bitumen tests here.
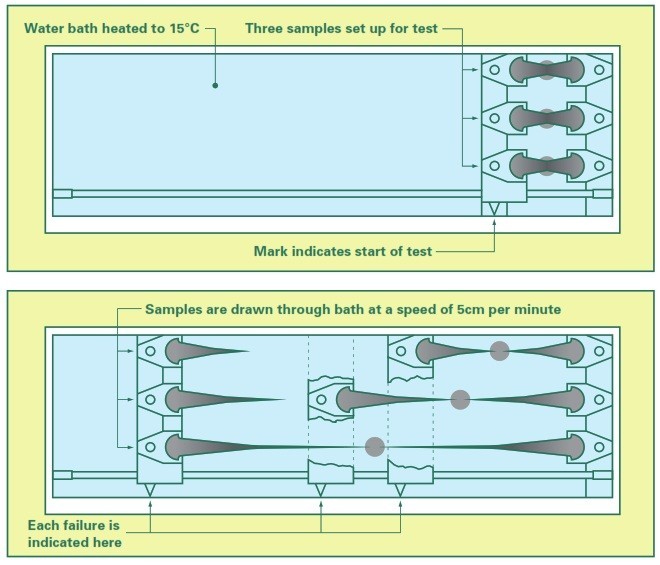
3- Penetration
The softness level of bitumen is indicated by entering a standard needle into it.
The harder the bitumen, the better it is for use in hot temperatures.
The standard range of penetration can vary among different grades of bitumen emulsion.
To learn more details about penetration testing, check out here.
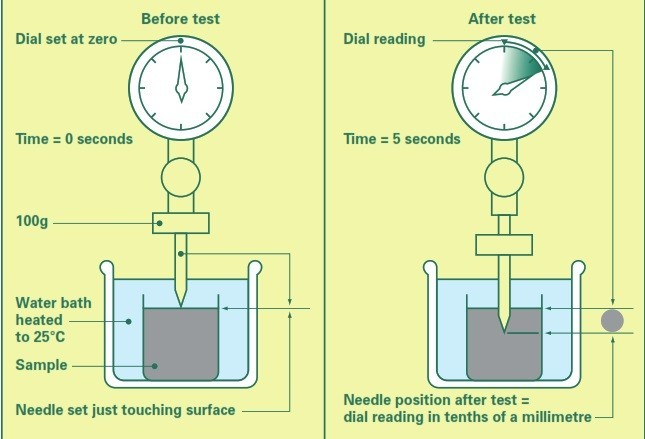
4- Storage stability
This parameter evaluates the stability of bitumen emulsion during the storage.Known also as sedimentation, storage stability shows if the bitumen emulsion droplets settle after manufacturing or not.
For testing the sedimentation of bitumen emulsion, a sample of bitumen is stored in a cylinder at room temperature.
After 24 hours, two samples will be taken, one from the top of the cylinder and the other from the bottom. The weight of two samples will be compared at the next stage.
The difference between two samples’ weight should not exceed 1 unit.
Two main factors that affect the storage stability of bitumen emulsion are viscosity level and the droplet size.
A bitumen with smaller droplets has less risk of settlement.
5- Particle Charge
An emulsion’s anionic or cationic character can be determined by the particle charge test.
In this experiment, two positive and negative electrodes are placed inside the emulsion.
one of the electrodes, conducts a DC current through the emulsion in the container.
30 minutes later, electrodes are examined to determine which electrode has been covered with bitumen.
An anionic emulsion will sediment on the anode (positive electrode) while cationic emulsion will sediment on the cathode (negative electrode).

Bitumen Emulsion Application
In the early 20th century, bitumen emulsions were used mainly for spray applications, but nowadays they are also used for mixing and spraying in road construction and road maintenance.
This type of bitumen is used in various methods of road construction including tack coats, chip seals, slurry seals and micro surfacing.
More details about bitumen emulsion application are presented in the following.
- Tack Coat:
Bitumen emulsion especially CRS-1 and CRS-2 are the best choice for tack coats between layers of asphalt pavement.
They can be used to heavily improve the strength and fatigue life of asphalt pavement at a very low cost and it’s better to know that the use of cut back bitumen has been avoided.
For running tack coats, the best temperature is 10 to 15 degrees Celsius.
- Chip Seals:
It is possible to use bitumen emulsion to renovate and waterproof old roads.
Chip seals are one of the most cost-effective methods of pavement preservation, since they protect underlying pavement from oxidation and aging.
Generally speaking, chip seals are typically used on rural roads carrying lower traffic volumes.
- Slurry Seals:
In order to give a uniform texture to roads, engineers use slurry seals.
This mixture of bitumen emulsion, aggregates and mineral fillers is sprayed on the pavement to seal it and make the surface weather-resistant.
Slurry sealing is also used in the maintenance of asphalt pavements and it helps to reduce road surface damage due to bitumen oxidation, but cannot increase its structural strength.
- Micro Surfacing:
Micro surface is another form of slurry in road construction, which is composed of polymer modified bitumen emulsion.
The existence of dense-graded aggregates in this mixture makes it stronger and more durable than a slurry seal.
A specialized machine is used to apply the mixture on existing pavements, which carries all components and mixes them on-site. The mixture is then spread onto the road surface.
Must read: A review of different types of bitumen used for road construction
Advantages of Bitumen Emulsion to Cut Back
These bitumen emulsions are used in road constructions as a substitute for cut back bitumen and perform all the functions that cut back bitumen can perform.
- Bitumen emulsions are more economical than cutback bitumens. Because in most cases bitumen emulsions contain 60% bitumen and 40% water, while cut back bitumen contain 70% bitumen and 30% petroleum solvents such as kerosene, naphtha, diesel oil, etc. It is obvious that 40% water costs lower than 30% petroleum solvent.
- In comparison with cut back bitumen, it is not flammable.
- As emulsion mixes do not require hot mixing, the strength properties of bitumen are preserved. Cold mixing or only slightly heating of the emulsion ingredients is usually done for the construction of the pavement.
- Emulsions can be applied even when it’s raining in wet weather.
- Emulsions with lower viscosities are more spreadable and allow for better bitumen coating on aggregate surfaces.
- There is no waste in laying and storing.
- Compared to all building materials, it requires little or no energy to heat.
Disadvantages of Bitumen Emulsion
Since bitumen emulsions are a type of soluble bitumen, they can have disadvantages based on the solvent.
If it is soap or water based, it has no disadvantages, only its price is higher, when the mixture is poured on the ground, the water evaporates and the bitumen sticks as a binder.
But if it is based on gasoline solvent, when it evaporates, toxic substances such as sulfur remain in the environment, which causes diseases such as cancer.
Sometimes, in a long-term storage condition or when temperature changes are large, it may become two-phase and frangible.
Bitumen Emulsion Standard
In the US, two central institutions have defined and standardized bitumen emulsion classifications:
- The American Association of State Highway and Transportation Officials (AASHTO)
- The American Society for Testing and Materials (ASTM)
There are societies and institutions throughout the world that have standardized how bitumen emulsions are classified, identified, and tested.
These foreign institutions look up to AASHTO and ASTM and adapt their findings to the local context.
For example, in Brazil, the Brazilian Association of Technical Standards is the organization that is responsible for standardizing testing and classifications for all types of materials. Like emulsions, they adapt quality standards set by the American institutions to the reality of Brazil.
Sample of several bitumen emulsion standards are as follow:
- American standards :
- Anionic Emulsion: ASTM D977, AASHTO M140
- Cationic Emulsion: ASTM D2397, AASHTO M208
- En 12597
- IS 3117 (2004)
- BSI 434-2 (2006)
Bitumen Emulsion Packaging
For bitumen emulsion, there are several types of packaging, including :
- Barrel
- IBC
- Flexi tank
- Reconditioned drums
Other types of packing is not suitable for bitumen emulsion, but Infinity Galaxy provides your desired bitumen emulsion in the above packing.
Read More About Emulsion Bitumen:
Bitumen Emulsion Applications (Advantages and Disadvantages )
Bitumen Emulsion Supplier
FAQ
Are there any polymer- modified bitumen emulsion?
Yes. Altogether, there are different components like polymers, latex, acids and other materials that can be added to a bitumen emulsion to enhance its resistance at higher temperatures and make it stronger and more resistant to fatigue and rutting.
Are Bitumen Emulsions environmentally friendly?
Yes. Water is used to dilute bitumen emulsions which is an environmentally friendly solvent. Contrary to hydrocarbon solvents, which are harmful to the environment when used to dilute cutback bitumen.
How do we know that the bitumen emulsion has deteriorated?
It may take a few months after the purchase of bitumen to see if the bitumen has cracked. If the emulsion breaks, you will see the water and the bitumen separate.
Is it better to use bitumen emulsion or cut back bitumen?
It is better to use bitumen emulsions. It is more economical and easier to use and it is less dangerous than cutback bitumens.
What is the most important factor in testing bitumen emulsion?
The most important factor in bitumen emulsion testing is the percentage of bitumen. It directly affects the viscosity of bitumen emulsion.
What is the difference between ordinary bitumen and bitumen emulsion?
Bitumen emulsion is a chemical combination of bitumen, water, and an emulsifying agent. This liquefied bitumen is more efficient than ordinary bitumen for road construction, particularly at a lower temperature. With a lower viscosity in comparison to ordinary bitumen, this type of binder doesn’t need to be heated before being applied to the surface.
Do bitumen emulsions require any special maintenance?
Yes. Often, one of the main problems in the storage of bitumen emulsion is the storage environment. It should not be in contact with air. Neither should the tank be allowed to freeze. The type of tank that is used is also an important factor. Vertical tanks are superior to horizontal tanks because they minimize the surface area exposed to air. Horizontal tanks are acceptable but not recommended because they expose the emulsion to air at its surface. Also, prevent water and other foreign materials from getting into the bitumen storage tanks and maintain the quality and homogeneity of the mixture.
What is the exact function of emulsifiers?
Emulsifiers make emulsification easier by reducing the interfacial tension between the bitumen and water. It also stabilizes the emulsion by preventing the coalescence of droplets.
Which types of bitumen emulsion are most in demand?
CSS-1, RS-1, RS-2, CRS-1, K1-60 and K1-70 are the most demanding bitumen emulsions . East Asia has the highest demand for CSS-1 and CRS-1 , while Africa, Qatar, and the Persian Gulf countries have the highest demand for K1-60 and K1-70 bitumen emulsions.
What is non-ionic bitumen emulsion?
In this type of bitumen emulsion, Bentonite can be used as a mineral emulsifier. This non-ionic bitumen emulsion is not very common in road construction.
What is the difference between bitumen and emulsion?
1.Bitumen is obtained by distillation of the crude oil in the refinery, but emulsion bitumen is obtained from mixing bitumen, emulsifier and water. Bitumen is the base material of emulsion bitumen.
2.Bitumen is a semi solid material with high viscosity, but emulsion bitumen is liquid with very low viscosity.
3.Bitumen can be used as the main binder in the road asphalt, but emulsion bitumen can be used in the protective asphalt on the main asphalt of the road.
Infinity Galaxy, Bitumen Emulsion Supplier
The international bitumen emulsion supplier, Infinity Galaxy, is sending thousands of tones of bitumen emulsion in barrels to important ports around the world.
Infinity Galaxy built its business on values such as high quality products, competitive pricing, satisfied customers, and efficient logistic services.
We can pack and export your needed bitumen in the shortest possible amount of time.
If you want to know more about bitumen emulsion and the purchasing terms, you can contact us or fill out our inquiry forms.
"*" indicates required fields