Direct reduced iron (DRI) also known as sponge iron, is a product of direct reduction of iron ore in various forms such as lumps, pellets, or fines. About 5% of global steel is produced from sponge iron (DRI), and this trend is increasing. Through the direct reduction of iron ore, oxygen is expelled from the iron to make metallic iron. Sponge iron is an essential raw material for making iron and steel products, and it suitably replaces scrap and blast furnaces.
The History of Sponge Iron
The earliest methods of sponge iron production relate to the Middle East, Egypt, and Europe to achieve iron. In China, they had applied the bloomery method and the blast furnaces to obtain sponge iron. Although, in the traditional method the furnace temperature is low and about 1,100 °C, just a small quantity gets produced each round in the blast furnace.
Comparing to the traditional technique, the direct reduced iron method is more fuel-efficient in steel production. Moreover, DRI plants should not be a part of an integrated steel plant, unlike the blast furnaces. Additionally, direct reduced iron plants are more economically efficient as they require less initial capital in contrast with integrated steel plants. Hence, in mini steel plants, producers profoundly prefer to use direct reduced iron instead of the blast furnace. Direct reduced iron is extremely suitable for developing countries with limited high-grade coking coal supplies.
The Direct Reduction Process
The direct reduction process aims to drive off the oxygen from all forms of the iron ore without melting it. It means the process’s temperature must stay below the iron melting point (1,538 °C). The furnace heat is typically in the critical point in the range of 800–1200 °C. The process includes two methods, gas-based and coal-based. Depending on the dominant sources of the countries in gas or coal, producers chose one of the methods.
Four various procedures of direct reduced iron exist but generally, the pellet, lumps, or fines of the iron ore, in the rotary kiln, confront the gaseous reductants which are a mixture of hydrogen and carbon monoxide. Through some other chemical processes, the oxygen is removed, metallization happens and the final sponge iron turns out.
The quality of the sponge iron relates to the amount of oxygen exploited from the iron ore and the purity of the primary iron ore which is regularly around 67%. The purity of the iron (Fe) in the final direct reduced iron is about 84 to 95%. It means sponge iron is a proper raw material for steel.
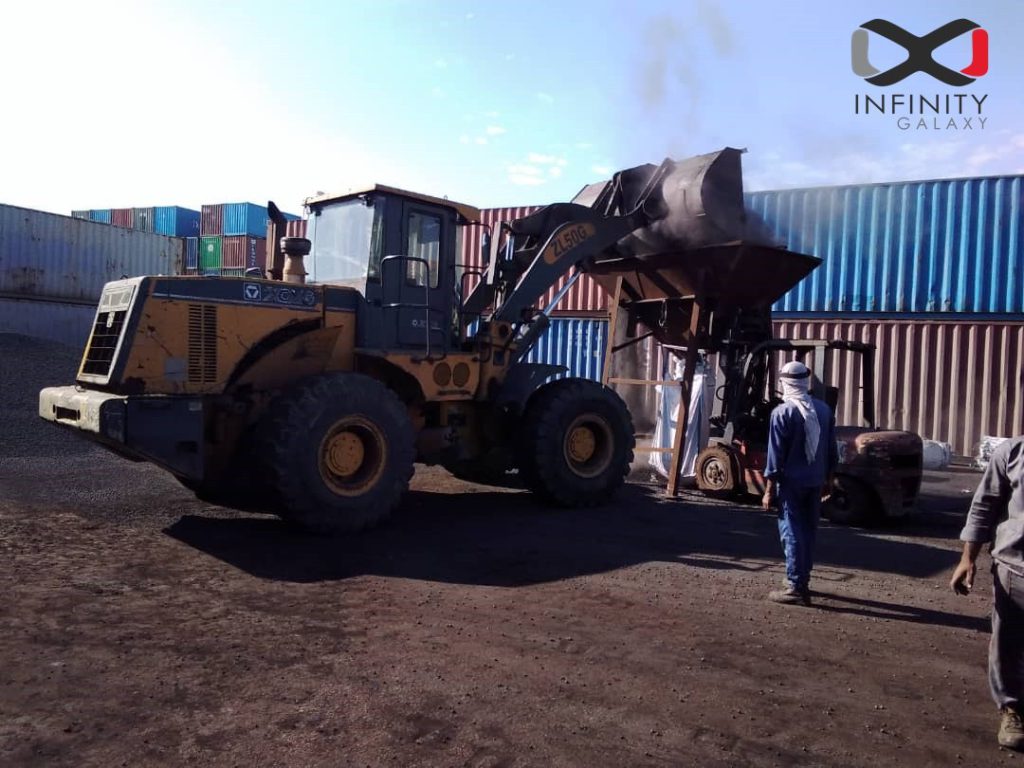
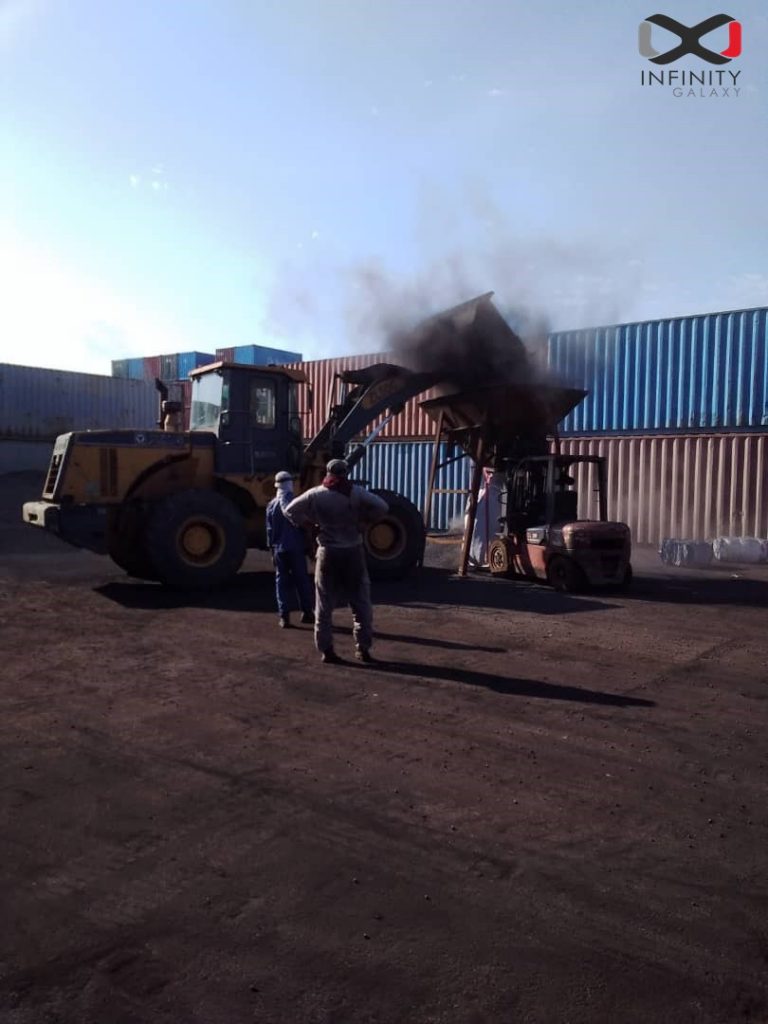
Scrap vs Direct Reduced Iron
Iron is a reversible metal which means we can melt iron products again as scrap. Steel and iron recycling is environment-friendly and almost profitable. Recent global scrap metal recycling has been estimated at 895.8 Million Metric Tons in the year 2020. Steel scrap is nearly the most recycled material. Numerous of our daily consuming materials contain aluminum, steel, or other metals. Products such as cans, food packaging, sprays, foils, and batteries are just some limited examples.
Steel scrap recycling is energy-saving and reduces the environmental footprints of metal mining. But there are several downsides to recycling.
Manually separating metal materials from plastic and other components is one of the pitfalls of recycling. Additionally, with every recycling process, the produced metal degrades. The quality is no longer likewise the former.
Sponge iron, on the contrary, is a quick method. It does not need manual separation and directly reduces oxygen from iron ore in the metalizing process without melting the iron. We also know, initiating direct reduced plants are more economic and unchallenged. It adequately substitutes scrap in steel production. Instead of melting the steel scraps in mini steel plants, sponge iron dissolves in an electric arc furnace/induction furnace to create steel.
Loading Sponge Iron from Port
Sponge Iron Usage and Benefits
Direct reduced iron has a high degree of “Fe” and metallization with consistent quality and less Sulphur & Phosphorus. It has impurities but they are insignificant.
Sponge iron, therefore, substitutes scrap in steel production. Instead of melting the steel scraps in mini steel plants, sponge iron dissolves in an electric arc furnace/induction furnace to create steel.
Direct reduced iron has different sizes and forms and all of them are easy to convey in plants of transferring to other locations.
The sponge iron gets heavily hammered and welded together to produce wrought iron. This wrought iron has about 3% slag and a small percent of other impurities. If the treatment continues, other heat treatments such as steeling can proceed.
Moreover, in the Integrated Steel Plants, sponge iron acts as a coolant of LD converters.
Sponge iron is highly similar to pig iron, so it can be a suitable alternative feedstock for the electric furnaces in smaller factories. By using Direct reduced iron, they can decrease scrap consumption and produce higher quality steel.
Besides all the benefits of sponge iron, it is prone to oxidization and rusting. After producing the sponge iron, producers proceed with the steel manufacturing process as quick as possible to avoid rusting.
Inspection Report of Sponge Iron
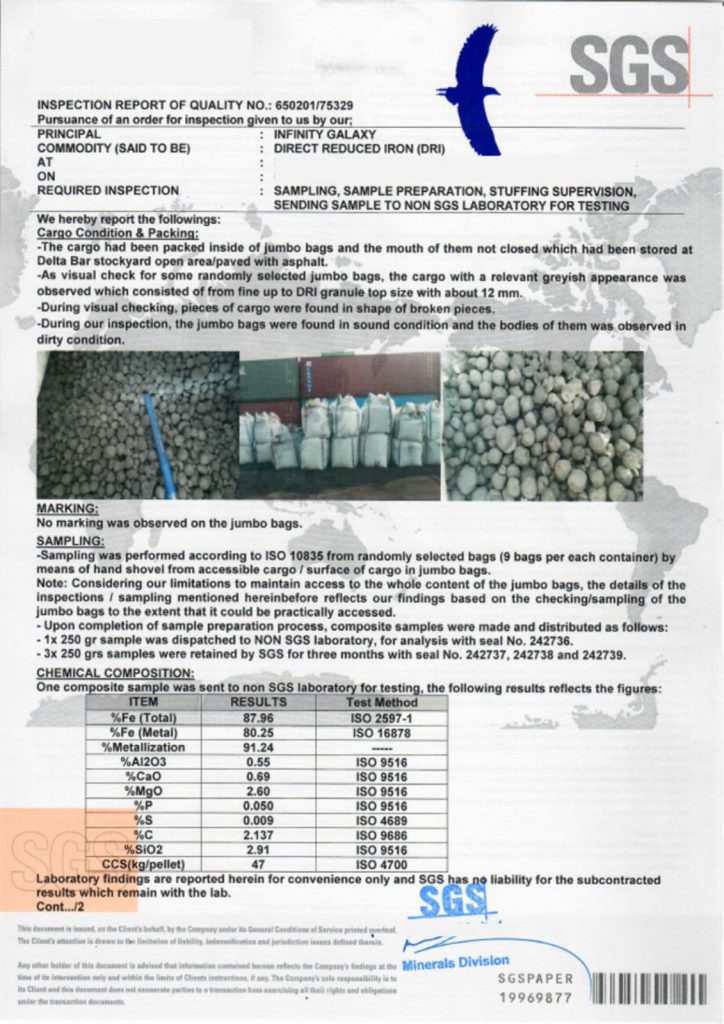
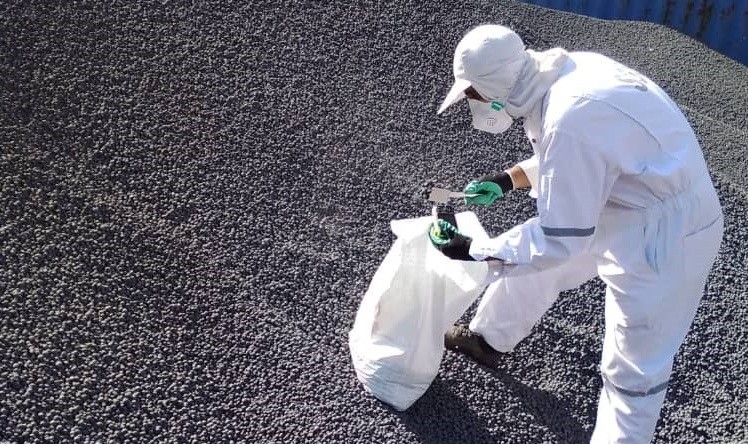
Sponge Iron Grades and Specification
Sponge iron can have various specifications, and typically they contain slag or Gangue. However, the impurity is insignificant and does not damage production processes. Several grades of sponge iron include:
GRADE – A (FeM – 81% Min)
GRADE – B (FeM – 78 To 80 %)
GRADE – C (Fem – < 78%)
Infinity Galaxy provides high-grade sponge iron with consistent quality. For more information and prices, please contact us.