Base oil properties have a direct impact on the overall performance and lifetime of lubricants.
To correctly transfer, maintain, and use the base oils, we have to first know their properties.
In general, base oil properties are divided into two categories: physical and chemical, which will be explained further.
This article gives you the most important information about base oil properties that you need for selecting your desired base oil.
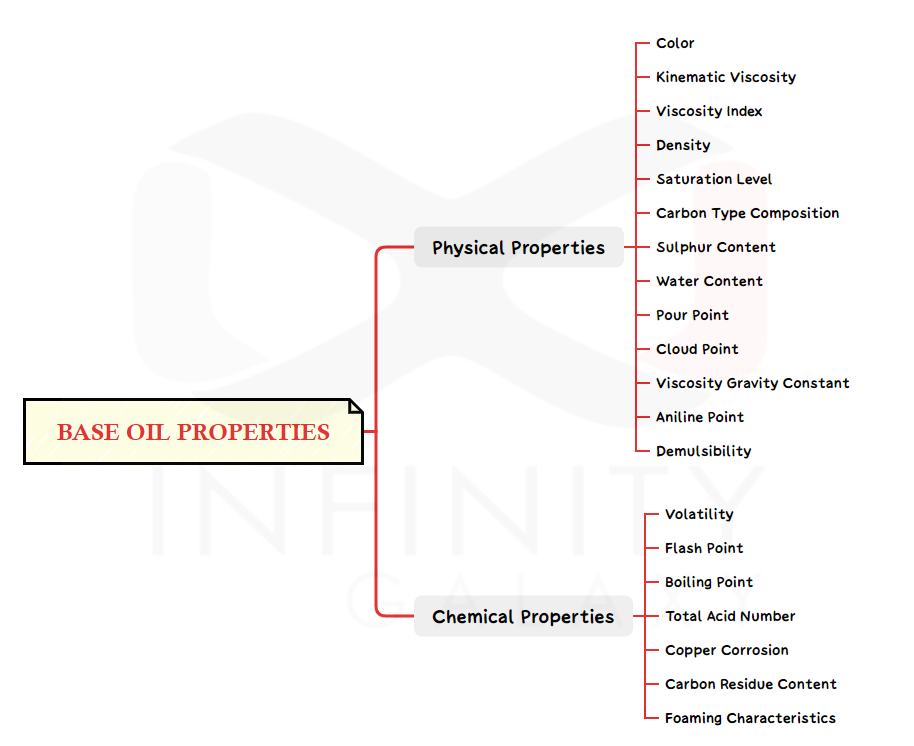
Physical Properties
Appearance
Color (Test method: ASTM D1500)
The color of the base oil is an important quality control indicator. It is easily checked by the user or SGS agent inspector.
The color of base oil can show contamination. If there are many impurities, such as sulfur and nitrogen, in the base oil, the viscosity index decreases and the color of the oil becomes darker.
Although color is not the only important factor in evaluating base oil quality, the ASTM D1500 color test results are numbers in the range of 0.5-8, which respectively indicate a change in color from light yellow to dark red.
That means if the test result for a base oil is 8, its color is very dark and it has a lot of impurities.
Viscosity
Kinematic Viscosity (Test method: ASTM D445)
Kinematic viscosity of the base oil is its resistance to flow. The suitable viscosity of the base oil causes it to perform well when used in industrial equipment. This will reduce the costs related to engine and machine repairs.
The viscosity should be proportional to the speed, pressure and temperature conditions of the operation. Low viscosity makes the lubricating film move quickly and with the least resistance. As a result, it cannot create enough resistance to cope with pressures or stresses.
The viscosity report is meaningless without mentioning the temperature; therefore, to measure the viscosity index, viscosity is usually reported at both 40°C and 100°C.
Viscosity Index (Test method: ASTM D2270)
Viscosity index is one of the most important and essential properties of base oil. In general, the viscosity of oils decreases with increasing temperature and they become more fluid. This change in viscosity with temperature is determined by the viscosity index or VI.
The higher the viscosity index, it means that the viscosity of that oil is more stable and has fewer variations compared to temperature changes. For this reason, oil with a high viscosity index maintains its lubrication properties in very high or even very low temperature conditions.
In industrial equipment where the internal parts are in contact with each other at high speed, a lot of heat is generated and these parts get hot. If a base oil with a low viscosity index is used in this situation, the lubricating properties of the base oil will be lost and it will damage the parts.
Generally, an increase in base oil purity will always be accompanied by an increase in viscosity index. The high VI base oil has a higher cost compared to low VI base oil.
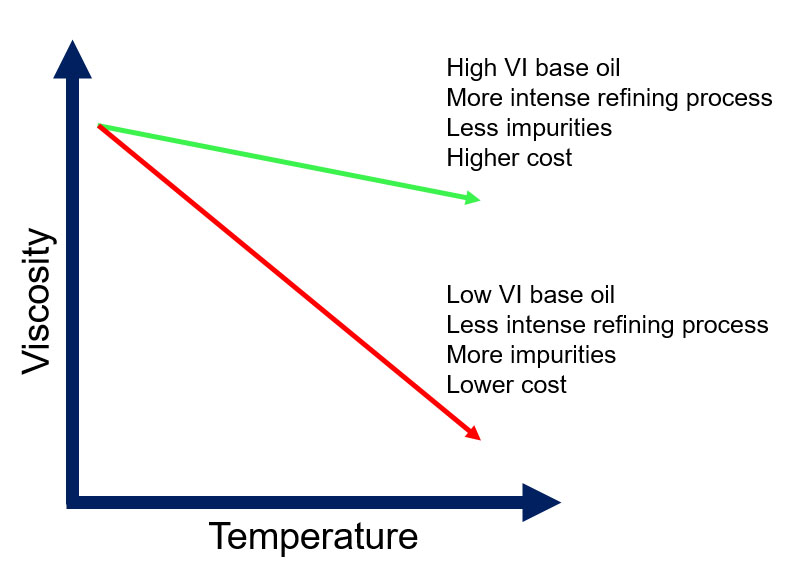
Density
Density (Test method: ASTM D1298)
Density means mass per unit volume. For example, in the same volume of oil and water, the oil density is lower so it floats on the water.
Moreover, by increasing the density of the base oil, the viscosity also rises, which means an increase in resistance to flow.
Composition & Purity
Saturation level (Test method: ASTM D2007)
Saturates are a type of molecule commonly found in base oil. They are naturally present in the base oil, but higher levels of saturation are achieved during the refining process.
A higher percentage of saturation indicates an improvement in the quality of the refining process. If the level of saturation is higher, the molecular bond of the oil is stronger. This increases base oil resistance to destruction and base oil oxidation.
Carbon type composition (Test method: ASTM D2140)
The carbon type composition in base oil gives a lot of information about its characteristics. CA, CN and CP show the percentage of aromatic, naphthenic and paraffinic compounds, respectively.
The high percentage of aromatic compounds shows the low quality of base oil. Naphthenic compounds in the base oil make it possible to use it at lower temperatures and increase the solubility of additives. On the other hand, paraffinic compounds make it possible to operate at higher temperatures and have a higher viscosity index.
Therefore, according to the use of base oil, its composition should be carefully considered.
Sulphur Content (Test method: ASTM D2622)
Sulfur compounds and aromatic structures are unstable and they frequently react quickly with oxygen.
This issue leads to acid formation and increased equipment corrosion. Also burning a fuel containing sulfur produces sulfur dioxide, a highly irritating gas that is harmful to animals, plants, and a major source of air pollution.
By improving the base oil refining process, sulfur is removed and pure oil is prepared at a higher price.
Water Content (Test method: ASTM D1744)
Water can exist in base oil in three forms: free, emulsified, and dissolved. When oil mixes with water, it leads to the production of undesirable byproducts.
Also, the presence of water in lubricants reduces the stability of the oil film in equipment and increases the corrosion and rusting of machines.
Low Temperature Properties
Pour Point (Test method: ASTM D97)
The lowest temperature at which a sample of base oil can be flowed by gravity determines the pour point. Pour point is about 3-5°C higher than the solidification point.
Base oil with a lower pour point is suitable for low-temperature conditions. Depending on the type of base oil, the pour point can have a range from -65°C to -2°C.
More naphthenic compounds in the base oil lead to a lower pour point, while the presence of paraffinic compounds increases the base oil pour point.
Cloud Point (Test method: ASTM D2500)
The cloud point is defined as the temperature at which components with a high tendency to solidify start crystallizing and solidifying.
The cloud point is the lowest temperature at which the oil can be used, and is usually higher than the pour point.
Paraffinic compounds would like to crystallize, so their increase in the base oil leads to an increase in cloud temperature. While naphthenic compounds have a low tendency to crystallize, their presence reduces the cloud temperature.
Solubility
Viscosity Gravity Constant (VGC) (Test method: ASTM D2501)
VGC is an indicator of base oil composition and solubility. It’s a dimensionless number between 0.8-1. When it is close to 1.00, the base oil has a higher aromatic content, and values near 0.800 confirm paraffinic materials.
Aniline Point (Test method: ASTM D611)
Aniline point is also a property that indicates the solubility of a base oil. It is defined as the lowest temperature at which the base oil is completely miscible with an equal volume of aniline.
While paraffinic base oil has a high aniline point (approximately 100°C or greater), naphthenic or aromatic base oils have a low aniline point (less than 100°C). The lower the aniline point, the better the solubility.
Other
Demulsibility (Test method: ASTM D1401)
Demulsibility is the ability of base oil to separate from water. A high demulsibility rating means that the base oil will resist forming an emulsion with water.
Base oil contamination with water reduces the stability of the oil film in equipment, increasing corrosion and foaming.
In general, when there is water and humidity in the operating conditions, the demulsibility should be monitored.
Chemical Properties
Safety and Volatility
NOACK (Test method: ASTM D5800)
The NOACK is a widely accepted method of measuring volatility. The NOACK volatility test determines how much a base oil evaporates at high temperatures.
A higher evaporation rate leads to an increase in the viscosity of the remaining oil, oil consumption and emission of pollutants.
Flash Point (Test method: ASTM D 92 & 93)
The flash point is the minimum temperature at which a base oil creates flammable vapors.
A lower flash point indicates that the base oil is more volatile and ignitable. Knowing the flash point of the base oil can greatly reduce the risk of fire during transportation, storage and maintenance.
Flash points can be shown as COC and PMOC in the base oil properties table. The ASTM D92 method measures the flash point by the Cleveland Open Cup Tester (COC) and the ASTM D93 method uses the Pensky-Martens Closed Cup Tester (PMCC).
Boiling Point (Test method: ASTM D7500)
The base oil consists of many components, so it doesn’t have a single boiling point. The Initial Boiling Point (IBP) and the final boiling point (FBP) form the boiling point distribution.
Base oils with high boiling range distribution produce more combustion deposits. And it can lead to failure and blocking of equipment and engines. On the other hand, very high volatility and very low boiling point distribution leads to high oil consumption.
Oxidation Stability
TAN (Total Acid Number) (Test method: ASTM D664)
Oxidation is a chemical reaction that occurs with a combination of the base oil and oxygen. Calculation of the total acid number is one of the methods by which the oxidation stability of the oil is evaluated.
Base oil may contain acidic components that are created by additives. The rate of oxidation is accelerated by high temperature, water, acids and catalysts such as copper. Oxidation leads to an increase in oil viscosity, solid deposits and sludge.
Corrosion
Copper Corrosion (Test method: ASTM D130)
Measuring the corrosion rate of copper in a base oil is designed by the ASTM D130 method. Corrosion usually caused by active sulfur compounds. The test results are shown in the form of 1a-1b, 2a-2e, 3a-3b and 4a-4c scales.
1a indicates slight discoloration and 4C indicates severe corrosion. This analysis method only shows the corrosive effects of oil on copper alloys, and does not provide information on corrosion on iron or ferrous parts and components.
Other
Carbon Residue Content (Test method: ASTM D 189 & 524)
Colloid, asphaltene, and polycyclic aromatic hydrocarbons are the primary components in the creation of carbon residue in base oil. Because they easily breakdown and condense to residual carbon in low-oxygen environments.
The amount of residual carbon is also used to assess the degree of refining in base oil production. The evaluation of the carbon residue content may be shown in one of the two methods, Conradson carbon residue (ASTM D189) or Ramsbottom carbon residue (ASTM D524) in the base oil properties table.
Foaming (Test method: ASTM D892)
Oil foaming may be a severe issue in high-speed, high-volume pumping and lubricating systems.
Air bubbles in the base oil cause faster oxidation and a reduction in its lubricating ability. The results of the ASTM D892 test are shown in x/y form.
For example, 20/0 means 20 milliliters of foam was measured after 5 minutes of aeration followed by no foam stability (0 ml) after the 10 minute settling time.