Understanding the base oil production process is crucial in determining its quality and price. Generally, there are two main types of base oils: mineral and synthetic. Both are made naturally from crude oil.
To make synthetic base oil, crude oil is used in an indirect way, and one of its derivatives is used in the synthesis process. But Mineral base oil is produced directly from crude oil refining.
Several production methods, like solvent refining or hydrocracking, result in different degrees of purity and product grades.
This article gives you information about different base oil production processes and their impact on base oil quality.
Mineral Base Oil Production Process
Mineral Base oil is produced and purified in the oil refining unit. The two main input streams to this unit are lube cuts and deasphalted oil.
Lube cut is one of the products from vacuum towers that are directly transferred to oil refining units.
On the other hand, for producing deasphalted oil, the vacuum tower residue passes the deasphalting unit. Then deasphalted oil transferred to the base oil manufacturing process unit.
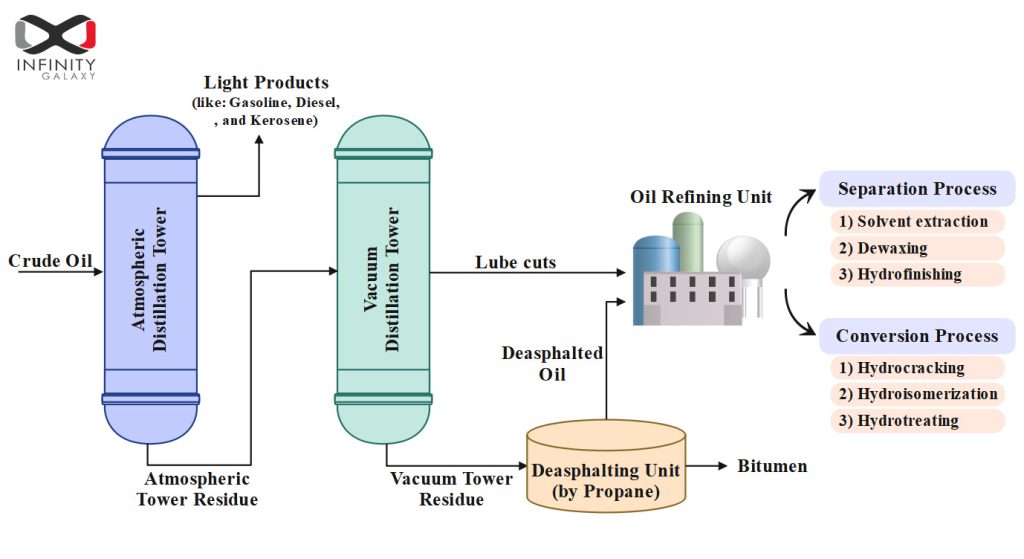
In the oil refining unit, operations are carried out to improve the base oil properties, including temperature properties, viscosity, stability against oxidation, and color.
In addition, these processes help to remove undesirable compounds such as aromatics, sulfur, and waxes.
Different methods and conditions of the oil refining process make various grades of base oil.
Generally, there are five main groups for base oils based on their viscosity, saturate content, sulfur content, and other factors. The first three groups are mineral oils, and their purity and quality improve from groups 1 to 3. For more details, see the base oil article.
Two main methods are used in oil refining units to produce base oil :
- Separation process
- Conversion process
Separation Process
This method is based on solvent extraction, in which there is always a product and a byproduct. Refineries that were built at the beginning of the 20th century often use this technique.
The solvent extraction method has a lower operating cost than the conversion method and is generally used to prepare low-grade base oils (Group 1).
It consists of three stages:
- Solvent extraction
- Dewaxing
- Hydrofinishing
Explanations for each are provided below:
1- Solvent Extraction
The main purpose of this step is to remove aromatic compounds and increase the oil’s resistance to oxidation. Phenol or furfural is generally used as a suitable solvent in this process.
The solvent dissolves the undesirable compounds in itself, and two streams of product and byproduct are created.
The byproduct is rich in aromatic compounds that are used as aromatic rubber process oils. The product flow, which contains the main base oil, is transferred to the dewaxing unit.
2- Dewaxing
Waxes are linear paraffin compounds that solidify at temperatures below 50°C. As a result, removing them is very important for improving the low-temperature properties of base oils, especially the pour point.
This process is done using methyl ethyl ketone and toluene in the combined method of extraction and crystallization.
The byproduct of this process is completely paraffin, and its main product is base oil containing naphthenic and paraffinic compounds and some aromatics.
This oil is generally in group 1 base oils and is used in some industries.But for making group 2 and 3 base oils, the dewaxed base oil is also transferred to the hydrofinishing unit.
Visit base oil applications article to read about the usage of base oil in various industries.
3- Hydrofinishing
The hydrofinishing process is used to remove polar compounds such as sulfur and nitrogen from the base oil.
In this step, a chemical reaction occurs using a catalyst and hydrogen at high temperature and pressure. The quality of the base oil gets better as the temperature and pressure increase in this process.
The resulting product has a high viscosity index (VI), more stability against oxidation, a lighter color, and a lower sulfur percentage.
The base oil produced at this unit has high quality and is used in sensitive industrial machines and devices, aviation, marine, and other advanced industries.
Conversion Process
This process involves converting undesirable products into desirable products using catalyst, hydrogen, heat, and pressure.
One of the benefits of this method is that no unwanted byproducts are produced, and 100% of the input feed is transformed into high-quality base oil.
The conversion process consists of three steps that result in high-quality base oil from groups 2 and 3:
- Hydrocracking
- Hydroisomerization
- Hydrotreating
In the below, we have explain each one:
1- Hydrocracking
Hydrocracking is a chemical reaction at high temperature and pressure (420°C, 200 bar) that involves breaking down the larger,and more complex molecules (naphthene and aromatic structures) into smaller, simpler,and more uniform compounds.
2- Hydroisomerization
This step is also known as hydrodewaxing, which changes normal paraffin wax compounds into desirable isoparaffin structures.
Isoparaffins are liquid at room temperature and have lower freezing point than normal paraffins. So this process could decrease the pour point of the base oil to a range of -10°C to -40°C. This step not only makes the oil better at low temperatures, but it also makes it more resistant to oxidation.
3- Hydrotreating
Hydrotreating completes the previous two-stage operation by totally removing all of the unwanted components, like sulfur and nitrogen, from the base oil.
The hydrocracking and hydroisomerization processes involve breaking chemical bonds, which reduces the stability of the base oil. At this stage, by using more hydrogen, the bonds are fully saturated, and the base oil is prepared with high stability.
Synthetic Base Oil Production Process
Synthetic base oils are made artificially by chemical reactions. In this chemical process, new molecules and structures are made in such a way that they have the desired properties for a high-quality base oil.
However, its base material is still petroleum derivatives (e.g., ethylene) that are physically and chemically modified. The actual synthesis process and composition of additives are unique to each company and vary among manufacturers.
We hope this article was helpful for you. If you have any questions or suggestions, leave a comment.